Intelligentization of the greenhouse with PLC & SCADA
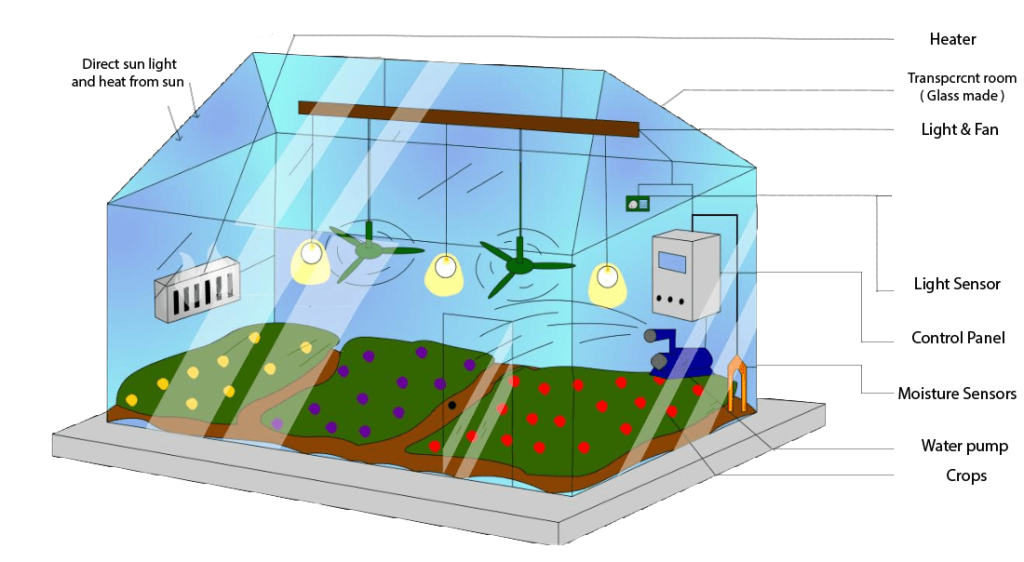
Introduction
Farmers do not know the exact weather conditions, so the activity done by them is not accurate. They perform their activity according to observations and experience, so different results are obtained each time.
An intelligent system is used to make accurate conclusions about the activities that should be done in greenhouses by farmers under different environmental conditions.
Productivity can be increased by using greenhouse automation. This system is based on the monitoring and control of parameters that play an important role in the greenhouse. When the sensors reach a certain threshold, it sends a signal to the microprocessor, the microprocessor processes that signal and takes appropriate actions.
For proper and fast growth of various plants, parameters are important for them. Plant growth depends on these parameters such as soil moisture, ambient humidity, temperature, etc. These parameters are controlled manually in the greenhouse to provide a suitable environment for plant growth. Greenhouse automation is designed to automatically control various parameters such as temperature, humidity, etc. This technique is one of the achievements of the intelligent agricultural system.
If the temperature, pressure, pH of the soil, etc. changes, the intelligent system helps to maintain or adjust that value in the appropriate way. This system reduces labor on parameter monitoring, and reduces process errors caused by manual control.
Greenhouses have various uses, most of which are growing vegetables outside the season, producing flowers and plants, adjusting the planting environment for the desired plant, producing fruit for the export market, and breeding plant species. These structures vary from small sizes to large industrial environments. A miniature greenhouse is known as a cold greenhouse. The interior of the greenhouse exposed to sunlight is significantly warmer than the outside temperature and protects the plants grown in cold weather. Many greenhouses or commercial greenhouses have high-tech production facilities for vegetables or flowers.
Glass greenhouses are equipped with screening facilities, heating, cooling, lighting, and may be controlled by a computer to optimize conditions for plant growth. The three environmental parameters are detected by sensors sensitive to temperature, humidity and light and are transferred to the PLC (Programmable Logic Controller) which stores the information in the database and is displayed on the PC.
Abstract
Greenhouse automation using PLC & SCADA can be considered a revolution in agriculture today. The introduction of this system can help increase the cultivated area in a controlled environment. Greenhouse environment, which is used to grow plants under controlled climatic conditions for efficient production, forms an important part of agriculture and horticulture sectors.
Suitable environmental conditions are necessary for optimal plant growth, improved crop yield and efficient use of water and other resources.
The automation of the process of obtaining data from various parameters that govern the growth of the plant provides the possibility of collecting information with the need of less labor.
Existing asset management systems are very expensive and difficult to maintain. This project is designed using PLC where temperature, humidity and lighting conditions are analyzed.
Greenhouse environmental performance
The explanations given in most sources about the temperature of the greenhouse are that solar rays (the visible part and adjacent to the infrared and ultraviolet ranges) pass through the roof of the greenhouse and are reflected and returned by the earth, and the long wavelengths in Inside the greenhouse, the glass and other materials used for greenhouse walls do not transmit infrared radiation, so infrared cannot pass through the radiation. Since the greenhouse space is not open for air movement, the heat cannot escape through convection, so the temperature inside the greenhouse increases. This is known as the “greenhouse effect”.
The greenhouse effect, due to the lack of air convection and the presence of infrared light in the environment, causes the increase of “greenhouse gases”, including carbon dioxide and methane, which further increases the photosynthesis of plants in greenhouses.
Greenhouse cooling may have economic consequences, according to studies. Analyzing the problems related to infrared rays in the greenhouse with plates with a high reflection coefficient, it can be concluded that the installation of such plates reduces the amount of heat by about 8%, and the use of colors on transparent surfaces is used to cover the roof of the greenhouse.
Low-reflective composite glass, or plain glass with an infrared filter coating, also saves money. In greenhouses in Iran, which use a roof with a plastic cover in most areas, they use a dark green cover (shade) due to the warming of the air.
Intelligentization with PLC
This system controls temperature, humidity and light intensity. The input includes sensors and transmitters, and the output includes irrigation pumps, electric valves, and motors for raising windows and blower fans. The overall control project is done by PLC.
The power supply is taken from the power lines (220V AC) and converted to 24V DC for PLC using SMPS or converter.
HT7S11 is a temperature sensor as well as a humidity sensor and transmitter to the controller. Programmable logic controllers (PLCs) have become an integral part of the industrial environment.
As a technician involved in PLC controlled processes, it is important to understand their basic features and capabilities. A programmable logic controller (PLC) is a digital computer used to automate electromechanical processes such as controlling machinery on factory assembly lines, amusement rides, or lighting fixtures.
PLCs are used in many industries and machines. Unlike general purpose computers, PLCs are designed for various input and output settings, temperature rise ranges, immunity to electrical noise, and resistance to vibration and shock.
In PLC, the executive programs to control the operation of the device are usually stored in memory with battery or non-voltage support. For example, the timing of receiving information is important because the output results must be produced in response to the input conditions in a limited time, otherwise the operation will give an unfavorable result.
Programmable Logic Controller (PLC)
All PLCs have the same basic components. These components work together to input information about the field to the PLC, evaluate that information, and send the information to various parts. Without any of these key components, the PLC will fail to function properly. The main components include the power supply, central processing unit (CPU) or processor, processor modules, input and output (I/O) modules, and peripherals.
How the system works
The type of input modules used by a PLC depends on the type of input device. For example, digital input modules are 0 or 1, while analog input modules respond to analog signals. In this case, analog signals represent the condition of the device or process as a wide range of voltage or current values.
The PLC input circuit converts the signals into logic signals that the CPU can use. The processor evaluates the state of inputs, outputs, and other variables by executing a stored program. It then sends signals to update the output status. Output modules receive control signals from the CPU and convert them into digital or analog values that can be used to control various output devices.
A programming device is used to enter or modify a PLC program or to monitor or modify stored values. After logging in, the program and associated variables are stored in the CPU. In addition to these basic elements, a PLC system may also include an operator interface device to simplify monitoring of the machine or process.
sensor
Sensors are basically current transmitters that transmit temperature and relative humidity input to two separate 4-20 mA current outputs. The relative humidity input is usually from 0 to 100% RH. The temperature is usually from 0 to 50 degrees Celsius. (Different domains are also available to be selected by referring to the required sensor catalog).
Blower fan
Fans are a device to move hot air out of the greenhouse to create a favorable climate for plants. When the air inside the greenhouse has reached the desired level, the fan is turned off, and when the temperature exceeds the fan, it turns on automatically.
Heating lamps
As you know, light is one of the main elements of photosynthesis. While photosynthesis typically involves sunlight, it can be simulated in indoor greenhouses or greenhouse environments using artificial lights.
To understand how to optimally use artificial lights for plant growth, it is better to review some other important terms related to photosynthesis. The first term discussed is light intensity. Lamps are devices that convert electric current into light. In addition to lighting up a dark space, they can be used for ambient lighting, signal lamps for electronic devices and heating lamps or (high pressure lamps) and many other things.
The goal in this project is to use high pressure lamps to increase the temperature. As the temperature decreases, high pressure lamps (240 volt lamps) are used to increase the temperature.
electric valve
Solenoid valves are very practical products that can be used in many diverse and unique applications in greenhouse systems. These valves are usually used as an alternative to manual valve replacement or in a location that cannot be accessed remotely. By stimulating the coil, the solenoid valve opens or closes the valve’s internal valve to allow or prevent flow.
SCADA (supervisory control and data acquisition)
SCADA is the abbreviation of the word control and monitoring of collected information. A computer system is used to collect and analyze data. SCADA systems are used to monitor and control plant or equipment in industries such as telecommunications, water and wastewater, electrical equipment, oil and gas refining, and transportation.
When the SCADA system is used for agricultural irrigation, the system can effectively monitor the output of any water connection equipped with solenoid valves of different capacities, improve equipment efficiency, monitor overall farm performance, monitor weather conditions, etc. Data and reduce the effects of freezing. By using this system, farmers can use many devices to irrigate crops at the same time, users can make adjustments such as temperature control, solenoid valve control, irrigation monitoring, water leakage control, and receive important information and review detailed reports.
Short circuit and system burn protection
Instead of old fuse types, a miniature circuit breaker is used in new constructions. Circuit breakers are small devices that are used to control and protect electrical panels and other devices from short circuits. They are used to maintain and ensure the safety and quality of supplied energy. Three-phase power is given from SMPS (switched-mode power supply) to MCB (miniature circuit breaker). In case of any problem in the 240V voltage, the MCB will shut down and protect the entire circuit from serious damage.
Conclusion
Greenhouse automation is done with the purpose of providing a suitable environment for plants and preventing damage to plants from fluctuating environmental conditions. Automation in the greenhouse helps reduce labor with efficient output. The main goal of this project is to attract a healthy environment in unconventional farms and control the change of environmental conditions by using different components. This project has a wide scope in the field of modern agriculture.
References
- Sheetal K. Bhongle(2016). Greenhouse Automation for Agriculture Using PLC & SCADA International Journal of Innovative Research in Science, Engineering and Technology
- https://www.ijirset.com/upload/2016/december/31_Greenhouse.pdf